Introduction to Engineering Drawing Tolerance

In the world of engineering, precision is key. One of the essential aspects of creating accurate and reliable designs is understanding and implementing engineering drawing tolerance. This comprehensive guide will take you through the fundamentals of engineering drawing tolerance, providing you with the knowledge to ensure your designs meet the highest standards.
Engineering drawing tolerance plays a crucial role in defining the acceptable variations or deviations in the dimensions, form, and features of a manufactured part or assembly. It ensures that the final product aligns with the intended design specifications and can function properly within its intended application. By establishing tolerance limits, engineers can account for potential manufacturing variations and maintain the integrity of the design.
Throughout this tutorial, we will delve into the various aspects of engineering drawing tolerance, including its importance, types, and how to interpret and apply them effectively. Whether you are a novice or an experienced engineer, this guide will equip you with the skills to create precise and manufacturable designs.
Understanding the Basics

Before we dive into the specifics, let’s establish a solid foundation by understanding the fundamental concepts related to engineering drawing tolerance.
What is Engineering Drawing Tolerance?

Engineering drawing tolerance refers to the permissible range of variation allowed for a specific dimension or feature on a technical drawing. It defines the acceptable limits within which a manufactured part or component can deviate from its nominal or ideal value. These tolerances are essential to ensure that parts can be produced consistently and that they will fit and function as intended when assembled.
Importance of Engineering Drawing Tolerance

Engineering drawing tolerance serves multiple critical purposes:
- Ensuring Quality and Consistency: By specifying tolerance limits, engineers can control the variability in manufacturing processes, resulting in consistent and high-quality parts.
- Facilitating Assembly: Tolerances allow for proper fit and functionality when multiple parts are assembled together, ensuring smooth operation and minimizing interference or clearance issues.
- Managing Cost and Complexity: Properly defined tolerances strike a balance between precision and cost-effectiveness, allowing manufacturers to optimize production processes and reduce unnecessary complexities.
- Communication and Collaboration: Engineering drawing tolerance provides a standardized language for designers, manufacturers, and inspectors to communicate and collaborate effectively, ensuring a clear understanding of design requirements.
Types of Engineering Drawing Tolerance

Engineering drawing tolerance encompasses various types, each serving a specific purpose and applicable to different aspects of a design. Let’s explore the most common types:
Linear Tolerance
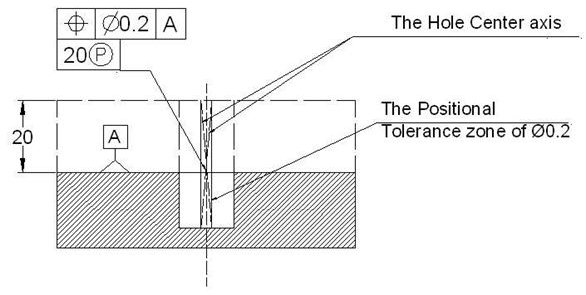
Linear tolerance, also known as geometric dimensioning and tolerancing (GD&T), specifies the permissible variation in the length, width, or height of a part or feature. It is typically represented by a dimension line with a tolerance value indicated by a plus-minus symbol (±). Linear tolerance ensures that the actual dimensions of the manufactured part fall within the specified range.
Angular Tolerance

Angular tolerance defines the acceptable variation in the angle between two intersecting lines or surfaces. It is commonly used in designs involving geometric relationships and ensures that the angles are within the specified limits. Angular tolerance is often represented by an arc symbol with the tolerance value indicated.
Form Tolerance
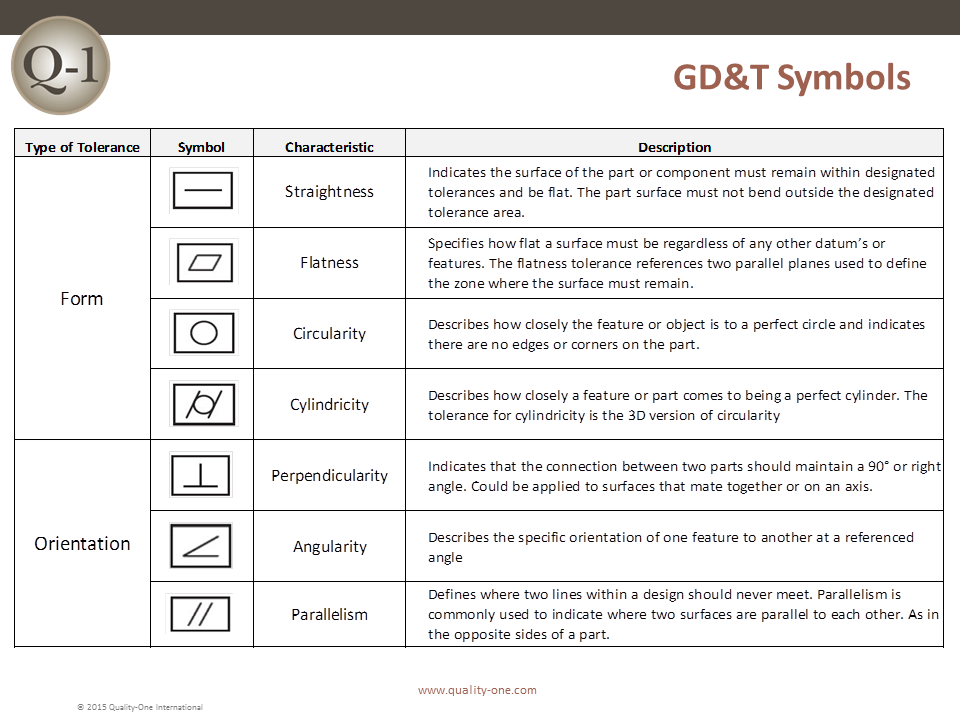
Form tolerance relates to the overall shape and profile of a part or feature. It includes concepts such as flatness, straightness, roundness, cylindricity, and more. Form tolerance ensures that the manufactured part maintains the intended shape and dimensions within the specified tolerance limits.
Orientation Tolerance

Orientation tolerance specifies the acceptable variation in the orientation or alignment of a part or feature relative to a reference datum. It ensures that the part is positioned correctly and aligned accurately with respect to other components in an assembly. Orientation tolerance is often represented by a symbol indicating the reference datum and the tolerance value.
Profile Tolerance

Profile tolerance defines the permissible variation in the shape or contour of a part or feature along its length or profile. It is commonly used for curved or complex shapes and ensures that the actual profile falls within the specified tolerance zone. Profile tolerance is typically represented by a tolerance zone symbol with the tolerance value indicated.
Interpreting Engineering Drawing Tolerance

Understanding how to interpret engineering drawing tolerance is crucial for accurate design and manufacturing. Let’s break down the process:
Reading Tolerance Specifications

When examining an engineering drawing, you will find tolerance specifications indicated near the dimensions or features they apply to. These specifications typically include:
- Nominal Dimension: The ideal or intended value of the dimension or feature.
- Tolerance Value: The range of acceptable variation around the nominal dimension.
- Tolerance Type: The type of tolerance being applied, such as linear, angular, or form tolerance.
- Tolerance Symbol: A symbol representing the specific type of tolerance, such as ± for linear tolerance or an arc for angular tolerance.
Understanding Tolerance Zones

Tolerance zones define the acceptable range of variation for a given dimension or feature. They are typically represented graphically on the engineering drawing. For linear tolerance, the tolerance zone is often depicted as a plus-minus symbol (±) with the tolerance value indicated. For other types of tolerance, such as angular or form tolerance, the tolerance zone may be represented by specific symbols or geometric shapes.
Applying Tolerance Principles

When applying engineering drawing tolerance, it is essential to consider the following principles:
- Select Appropriate Tolerances: Choose tolerance values that align with the functional requirements of the part or assembly, considering factors such as material properties, manufacturing processes, and intended application.
- Ensure Functionality: Tolerances should be defined in a way that ensures the part or assembly can perform its intended function without interference or clearance issues.
- Optimize Cost and Efficiency: Strive for the tightest tolerances necessary to achieve the desired functionality while considering cost-effectiveness and manufacturability.
- Consider Cumulative Effects: When designing complex assemblies, account for the cumulative effects of multiple tolerances to ensure overall functionality and compatibility.
Creating Engineering Drawings with Tolerance
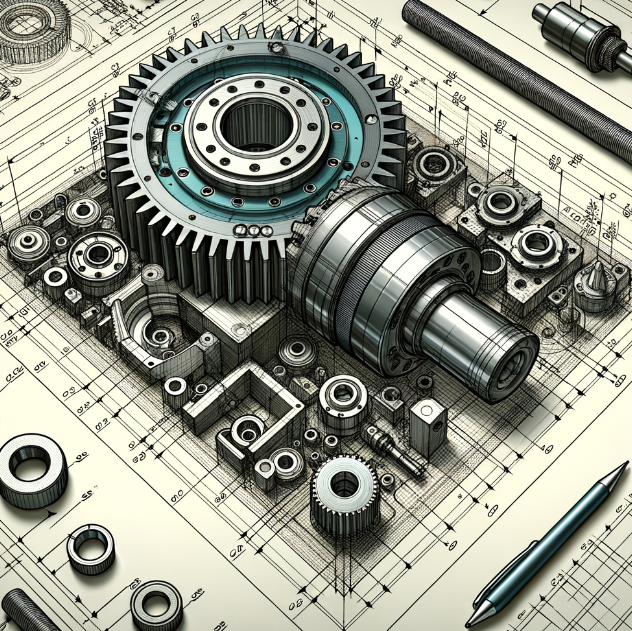
Creating engineering drawings that effectively communicate tolerance requirements is a critical skill for engineers. Here are some key considerations:
Using Standardized Symbols and Annotations
Utilize standardized symbols and annotations to represent different types of tolerance on your engineering drawings. This ensures consistency and clarity for all stakeholders involved in the manufacturing process.
Specifying Tolerance Values Clearly
Clearly indicate the tolerance values for each dimension or feature on your drawings. Use consistent formatting and ensure that the tolerance values are easily readable and understandable.
Providing Additional Notes and Instructions
Include additional notes and instructions on your drawings to provide further clarification or specific instructions related to tolerance. This can include information on how to measure or inspect certain features or any special considerations for manufacturing.
Applying Tolerance Stack-Up Analysis
Conduct tolerance stack-up analysis to assess the cumulative effects of multiple tolerances in complex assemblies. This analysis helps identify potential interference or clearance issues and ensures that the overall functionality of the assembly is maintained.
Common Tolerance Standards and Systems
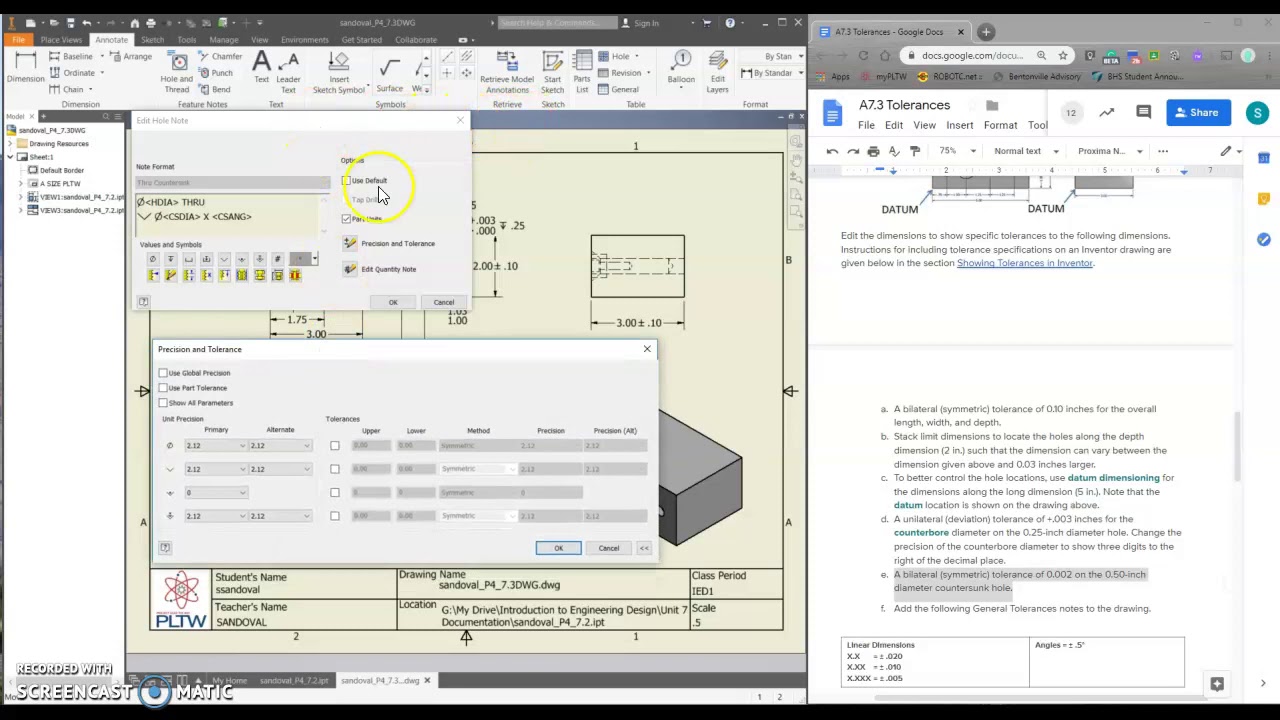
In the world of engineering, various tolerance standards and systems are used to ensure consistency and interoperability between different industries and regions. Let’s explore some of the most widely adopted tolerance standards:
ISO Tolerance System
The International Organization for Standardization (ISO) has developed a comprehensive tolerance system known as the ISO Tolerance System. This system provides a standardized framework for specifying tolerance grades and classes, making it easier for engineers and manufacturers to communicate and collaborate across different countries and industries.
ASME Y14.5 Standard
The American Society of Mechanical Engineers (ASME) has established the ASME Y14.5 standard, which is widely used in the United States and Canada. This standard provides guidelines for geometric dimensioning and tolerancing (GD&T), including the specification of tolerance grades, symbols, and application rules.
DIN and ISO 286 Standard
The Deutsches Institut für Normung (DIN) and ISO have collaborated to develop the ISO 286 standard, which is commonly used in Europe. This standard defines tolerance grades and classes for linear dimensions, providing a uniform approach to specifying tolerance limits.
JIS B 0401 Standard
The Japanese Industrial Standards (JIS) B 0401 standard is widely adopted in Japan and some Asian countries. This standard specifies tolerance grades and classes for linear dimensions, similar to the ISO 286 standard.
Implementing Tolerance in Manufacturing

Engineering drawing tolerance is not just a theoretical concept; it must be effectively implemented in the manufacturing process to ensure accurate and reliable production. Here’s how tolerance is considered in manufacturing:
Selecting Appropriate Manufacturing Processes
Different manufacturing processes have varying capabilities in terms of achieving specific tolerances. Engineers must carefully select the most suitable manufacturing processes based on the required tolerances and the nature of the part or assembly being produced.
Setting Up Machine Tools and Equipment
Machine tools and equipment must be properly calibrated and set up to achieve the desired tolerances. This includes adjusting cutting tools, fixtures, and other components to ensure precise and consistent machining.
Implementing Quality Control Measures
Quality control measures, such as inspection and testing, are essential to verify that the manufactured parts meet the specified tolerance requirements. This may involve using precision measuring instruments, performing statistical process control, and implementing error-proofing techniques.
Managing Tolerance Stack-Up
In complex assemblies, managing tolerance stack-up is crucial to ensure overall functionality. Engineers must consider the cumulative effects of multiple tolerances and implement design strategies to minimize potential interference or clearance issues.
Common Challenges and Solutions
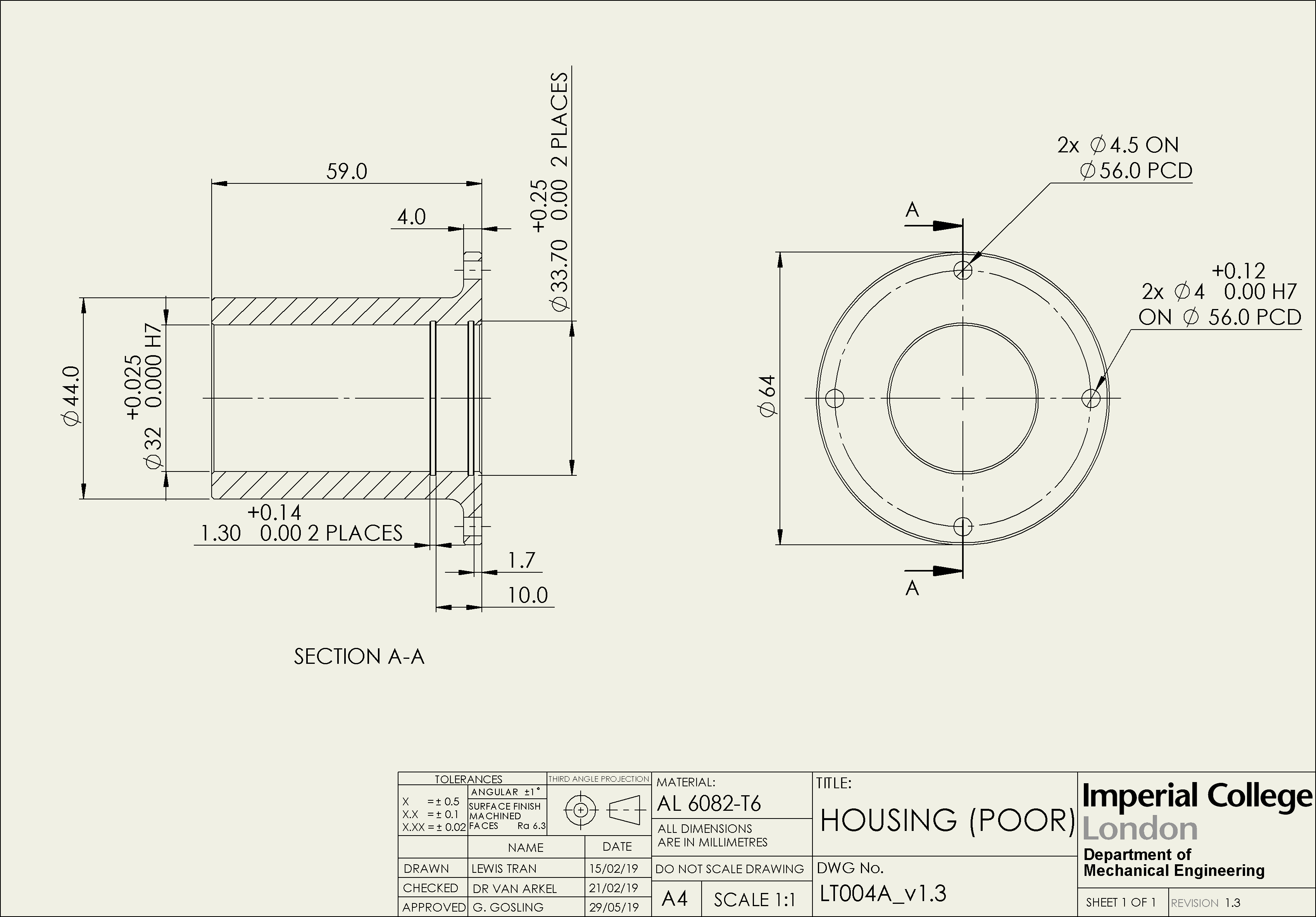
When working with engineering drawing tolerance, engineers may encounter various challenges. Here are some common challenges and potential solutions:
Tight Tolerance Requirements
Achieving extremely tight tolerance requirements can be challenging, especially for complex parts or high-precision applications. To address this, engineers can:
- Optimize Design: Review the design and explore opportunities to simplify complex features or reduce the number of critical dimensions.
- Select Advanced Manufacturing Processes: Utilize advanced manufacturing techniques, such as precision machining or additive manufacturing, to achieve tighter tolerances.
- Enhance Quality Control: Implement more rigorous quality control measures, including advanced inspection techniques and statistical process control.
Tolerances in Complex Assemblies
Managing tolerances in complex assemblies with multiple interconnected parts can be a significant challenge. To overcome this, engineers can:
- Conduct Tolerance Stack-Up Analysis: Perform thorough tolerance stack-up analysis to identify potential interference or clearance issues and optimize the design accordingly.
- Implement Error-Proofing Techniques: Use error-proofing techniques, such as poka-yoke or mistake-proofing, to prevent assembly errors and ensure proper alignment and functionality.
- Optimize Assembly Processes: Streamline the assembly process by implementing standardized procedures, clear instructions, and visual aids to minimize tolerance-related issues.
Communication and Collaboration
Effective communication and collaboration between engineers, designers, manufacturers, and inspectors are essential for successful tolerance implementation. To enhance communication, engineers can:
- Utilize Standardized Language: Adhere to standardized symbols, annotations, and terminology to ensure consistent understanding of tolerance requirements.
- Provide Detailed Documentation: Create comprehensive documentation, including drawings, specifications, and instructions, to facilitate clear communication and collaboration.
- Foster Open Communication Channels: Encourage open dialogue and feedback between all stakeholders to address any tolerance-related concerns or issues promptly.
Tips and Best Practices

To ensure the effective application of engineering drawing tolerance, consider the following tips and best practices:
- Define Tolerances Early in the Design Process: Establish tolerance requirements early on to guide the design and manufacturing process.
- Consider Functional Requirements: Always prioritize the functional requirements of the part or assembly when defining tolerances.
- Collaborate with Manufacturing Experts: Engage with manufacturing experts and seek their input to ensure that the specified tolerances are achievable and cost-effective.
- Conduct Regular Tolerance Reviews: Periodically review and assess the specified tolerances to ensure they remain aligned with the design goals and manufacturing capabilities.
- Stay Updated with Industry Standards: Stay informed about the latest tolerance standards and systems to maintain compatibility and interoperability with other industries.
Conclusion

Engineering drawing tolerance is a critical aspect of creating accurate and reliable designs. By understanding the different types of tolerance, interpreting tolerance specifications, and effectively implementing tolerance in manufacturing, engineers can ensure the production of high-quality parts and assemblies. Remember to prioritize functionality, collaborate with manufacturing experts, and stay updated with industry standards to achieve optimal results.
FAQ
What is the difference between linear tolerance and angular tolerance?
+Linear tolerance specifies the permissible variation in linear dimensions, such as length, width, or height. It ensures that the actual dimensions of a part fall within the specified range. Angular tolerance, on the other hand, defines the acceptable variation in angles between intersecting lines or surfaces. It ensures that the angles are within the specified limits.
How do I choose the appropriate tolerance values for my design?
+When choosing tolerance values, consider the functional requirements of the part or assembly, the intended application, and the capabilities of the manufacturing processes. Strike a balance between precision and cost-effectiveness, ensuring that the specified tolerances are achievable and do not introduce unnecessary complexities.
Can I use different tolerance standards in the same project?
+It is generally recommended to use a consistent tolerance standard throughout a project to avoid confusion and ensure compatibility. However, in certain cases, you may need to accommodate different tolerance standards based on the requirements of specific components or the preferences of different stakeholders. In such cases, clearly communicate the tolerance standards being used to avoid any misunderstandings.
How do I handle tolerance stack-up in complex assemblies?
+To manage tolerance stack-up in complex assemblies, conduct thorough tolerance stack-up analysis. This analysis involves evaluating the cumulative effects of multiple tolerances to identify potential interference or clearance issues. By understanding the tolerance stack-up, you can optimize the design, implement error-proofing techniques, and ensure the overall functionality of the assembly.
What are some common challenges when working with engineering drawing tolerance?
+Common challenges include achieving extremely tight tolerance requirements, managing tolerances in complex assemblies, and ensuring effective communication and collaboration between stakeholders. To overcome these challenges, engineers can optimize the design, select advanced manufacturing processes, implement quality control measures, and foster open communication channels.